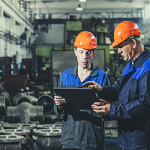
Change can feel like a leap into the unknown, a gamble fraught with risks. What if it flops? What if it dents our income or threatens our job security? It’s no wonder we humans cling to the familiar, preferring the devil we know over the one we don’t. Yet, when it comes to process improvement, there’s a flip side: it’s not just a necessity, but an exhilarating … [Read more...]