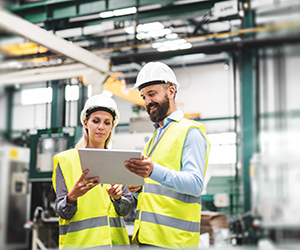
Six Sigma is quality.
Lean is speed.
The synergy of both is the most powerful engine available today to sustained value creation.
Lean Six Sigma is the ultimate formula for operational excellence, blending the precision of Six Sigma with the agility of Lean. Six Sigma, pioneered by Motorola, revolutionized quality control, gaining fame through adoption by giants like General Electric and Honeywell. Lean, rooted in the Toyota Production System, transformed production with its focus on speed and efficiency. Together, they form a dynamic synergy that drives unparalleled value creation. This powerful philosophy, now a cornerstone in manufacturing and beyond, empowers businesses to deliver high-quality results at lightning speed.
It was only a matter of time until the Six Sigma and Lean movements of the 2000’s merged together to form the Lean Six Sigma philosophy used today in most production facilities. But let’s investigate how Lean Six Sigma works but more importantly, how to implement it in an organization.
Lean Six Sigma Overview
The first half of the process, Six Sigma is a method that measures the variation of the outputs of a process, say the manufacturing of a widget. It measures the deviation of the outputs from a specified quality target, and uses Six Sigma “projects” to improve the process and reduce variation. The projects are structured around the acronym DMAIC (pronounced “De-may-ic”) which stands for Design – Measure – Analyze – Improve – Control. The goal is to get the process output variation to within 3 standard deviations from the mean in either direction, hence the name Six Sigma.
The other half of the process, Lean, turned manufacturing upside down. Rather than making sure the factory’s machines were running at maximum capacity, Lean changed the focus to the products. In Lean, the products are to be kept moving constantly through the assembly line, even if it meant machines were idle. Idle products were to be minimized rather than idle machinery. This meant that parts inventory was reduced to only what was needed at the time at each step (“just in time production”), and the value stream which considered the processes that add value to the product, were optimized rather than machine efficiency. Because slow processes are expensive processes, the combination of low inventory and fast payment by customers for products that needed a fraction of the time to get from initial raw materials to finished product, created vast financial gains.
Lean Six Sigma then, is the combination of the two.
Generally speaking, Six Sigma black and green belts are trained in lean. They create lean processes and measure lean cycle efficiency in addition to the regular Six Sigma metrics.
The DMAIC process improvement project system is adopted from Six Sigma, as are the Green, Black, and Master Black Belt specialists. The Six Sigma practitioners focus on the Lean concepts of value stream mapping and process cycle efficiency, that is, minimizing the amount of time that product is idling on or beside the assembly line (or maximizing the amount of time a product is being worked on in a value added way).
Also inherited from the Six Sigma side is the concept of organizational culture change.
Lean Six Sigma Culture
Six Sigma has as a central foundation the change of organizational culture to the new processes, and Lean Six Sigma retains this focus.
- Buy-in must start at the top. The CEO must be convinced of the effectiveness of the tools and demonstrate active engagement, not just passive acknowledgement.
- More than just a bunch of processes executed by trained professionals, a strong Six Sigma continuous improvement program succeeds because of the culture of the organization.
Lean Six Sigma Belts
Lean Six Sigma also retains the belt system of Six Sigma:
- Green belts are team members who work on Lean Six Sigma projects, implementing them into the processes of the organization. They use the tools in the DMAIC toolbox to complete the process improvement projects and report on the results.
- Black belts are responsible for delivering the value and benefits of Lean Six Sigma. They analyze data and decide which improvement projects are to be pursued. They lead the teams that implement change.
- Master Black Belts act as expert consultants or internal experts who are a resource to the black belts in the organization.
Lean Six Sigma Value Stream Mapping
Value stream mapping is the core concept of lean manufacturing that is inherited by Lean Six Sigma. The production plant is “mapped” into all the processes that occur to produce the finished product. Each step is drawn on a value stream map. At the bottom of the map, the Production Lead Time (PLT) and the Value Added Time (VAT) are plotted for each step, which tracks the amount of time within each production step the product is idling in inventory without being worked on in a value added way. Click on the sample Value Stream Map to the right to expand it.
The map is a living document that is continually consulted to determine the next improvement project. Each step is scrutinized to create the maximum amount of “flow”, and anything that stops the products from moving through the value added production line is waste, or “muda.” VAT should be maximized, and PLT should be minimized.
Once the value stream is defined the focus shifts to monitoring and controlling the the key metric in Lean, which is Cycle Efficiency.
Lean Six Sigma Cycle Efficiency
In a lean facility, product moves from raw material to finished good in the least amount of time. This eliminates inventory between production stations and allows the plant to rapidly switch product variants and/or adjust to changes in customer orders. It also minimizes the time between purchase of raw material and selling of the finished product, which can result in large one-time profits at the time the system is implemented. Unnecessary wait times between or at production stations are considered muda and must be aggressively eliminated. A lean factory has a small footprint because there is not much inventory waiting to be manufactured, hence the term “lean.”
The central measurement of the effectiveness of the Lean plant relates the amount of time spent on value added production on a product to its overall time moving through production.
- Value Added Time (VAT) is the amount of time spent adding value to the product. For example, bending a steel car door frame, or painting a furniture component.
- Production Lead Time (PLT) is the total amount of time from the start of the manufacturing process to the end.
Typical cycle efficiencies for various types of processes are:
Application | Typical | Lean |
---|---|---|
Machining | 1% | 20% |
Fabrication | 10% | 25% |
Assembly | 15% | 35% |
Business Processes – Transactional | 10% | 50% |
Business Processes – Creative/Cognitive | 5% | 25% |
The goal is 100% cycle efficiency, which means that the product is being worked on in a value added way right from the point it enters the facility as raw material to when it exits as a finished good. But realistically, cycle efficiency will never be 100% except for very simple processes with few production steps.
Lean Six Sigma Implementation
The implementation process of Lean Six Sigma in a new organization is inherited largely from the Six Sigma side, because it is much better developed.
- Management buy-in must be achieved. Lean Six Sigma, like standalone Six Sigma, cannot succeed without management support who provide a vision for its success.
- Corporate Strategy. Lean Six Sigma supports the goals of the organization. Most corporations have profit as a key metric, but there are other, underlying strategies of the organization which are usually pretty well defined. Non-profits and government agencies have the provision of a service as the main metric, but many define the underlying strategies similarly to a corporation. Lean Six Sigma supports those goals and must not be built as a separate initiative.
- Selection of Lean Six Sigma professionals from each department who act as the implementers of the program.
- Training of Lean Six Sigma professionals as black belts, green belts, or any other competencies as required.
- Optionally, a transforming event takes place to kick off the initiative and drive the corporate culture change.
Once the black belts and green belts are certified and ready to get to work on process improvement, specific projects can be identified.
Lean Six Sigma Project Identification
Selecting the right Lean Six Sigma process improvement projects is the key to a high Lean Six Sigma success rate. Black belts are released to measure and analyze the cycle efficiency of the organization’s processes. They perform Design of Experiments (DOE) to determine where process improvements are warranted. They analyze the data to determine the financial cost/savings as well as the effort required.
Lean Six Sigma projects are assembled and ranked according to priority, that is:
- Potential financial savings
- Effort required
Those that have the best return for the least effort become the highest priority.
Once the projects are identified, the black belts execute the projects using the familiar Six Sigma DMAIC guideline.
Lean Six Sigma DMAIC
Lean Six Sigma inherits the DMAIC acronym from Six Sigma. DMAIC represents the process which green and black belts go through to implement an improvement project. DMAIC stands for:
- Define
Confirm the opportunity, and define the boundaries and goals of the project. - Measure
Gather data to establish the current state, what is actually going on in the workplace and the process as it works today. - Analyze
Interpret the data and establish cause-and-effect relationships. - Improve
Develop solutions that are targeted at the confirmed root causes. - Control
Implement procedures that ensure the improvements and/or gains can be sustained.
As you can see, Lean and Six Sigma are tremendous compliments to each other.
Producing high quality products and services is important, and delivering them quickly is equally as important. But those who produce high quality, quickly, will reap the rewards.
Leave a Reply