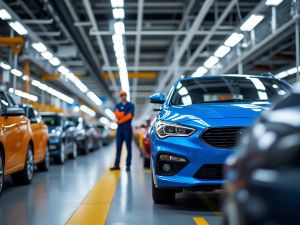
A google search for the term “lean project management” is a perplexity. At the time of this writing, the search results didn’t even attempt to place a result for lean methodology applications to project management until the bottom of the first page. Once there, the articles and courses that purport to teach lean project management as if lean was just another well established methodology in the toolbox of project management makes one wonder about click bait.
The reason for this is that the methodology referred to as “lean” was specifically developed by and for the manufacturing sector, which represents the polar opposite of projects which are temporary in nature and produce one, single product (or group of products) with a finite completion point.
Hence, the term itself, “lean project management” is actually an oxymoron, or at least the application of processes from one area to a completely opposite one.
That being said, it is without a doubt that Lean methodology has unmistakable applications to project management. Perhaps a manufacturing assembly line is really a series of projects performed ad infinitum. Or perhaps projects are just the creation of an assembly line that produces one product and then disbands.
Whatever the worldview, one cannot lose sight of the fact that the lean methods were not designed to apply to projects.
Originating from the Japanese manufacturing industry, particularly Toyota’s production system, Lean has transcended its roots to become a universal principle for eliminating waste and enhancing value in the “value stream.” Every action along the assembly line is producing value, and this value stream is the primary focus of lean efficiency improvements.
Here are a few ideas about how Lean can apply to project management:
Understanding Lean in Project Management
Lean isn’t about working harder; it’s about working smarter. At its core, Lean methodology aims to maximize customer value while minimizing waste. In project management, this translates to delivering projects that meet customer needs with minimal resources, time, and effort.
Waste in the production system is called ‘Muda.’ Muda is the enemy of productivity. Clearly, in the assembly line of a project, time or money that did not need to be spent to accomplish the project’s objective is also muda, and needs to be actively eliminated.
However, eliminating muda is not always as obvious as it sounds. From the arrival of parts at the assembly plant to their final placement within the finished product, minimizing the amount of transportation and storage, the aptly named just-in-time delivery, is an attempt within the manufacturing industry to reduce muda. A project manager, of course, must manage their project resources so as to produce the maximum amount of product or services with the least amount of resources as well. Any action within the project that is not required to produce the finished product is muda.
The Five Principles of Lean
To apply Lean in project management, one must understand and implement these five principles:
- Identify Value: What does the customer need? This involves direct communication and feedback loops with stakeholders to ensure the project’s deliverables are aligned with customer expectations.
- Map the Value Stream: Visualize the entire project lifecycle to identify every step that contributes to the final product. This helps in spotting redundant tasks or steps that do not add value.
- Create Flow: Ensure that once a project starts, it moves smoothly through each phase without unnecessary delays or interruptions. Techniques like Kanban boards can be instrumental here.
- Establish Pull: Instead of pushing projects through stages, let demand pull the work through the system. This means starting new tasks only when there’s capacity, reducing overproduction and waiting times.
- Seek Perfection: Continuous improvement is key. After each project, teams should reflect on what went well and what didn’t, making adjustments for future projects.
Lean Tools for Project Management
Lean accomplishes its value stream enhancement processes using a set of tools:
- Kanban: This visual system helps manage workflow by visualizing both the project’s progress and any bottlenecks.
- 5S: Sort, Set in order, Shine, Standardize, and Sustain. While originally from manufacturing, these steps can clean up and organize project documentation, tools, and processes for efficiency.
- Kaizen: Focuses on continuous, incremental improvements. Regular, small adjustments keep the project lean and adaptable.
- Value Stream Mapping: Helps in identifying waste in the process and understanding the flow of value from start to finish.
Benefits of Lean in Project Management
- Increased Efficiency: By focusing on value and eliminating waste, projects can be completed faster with fewer resources.
- Enhanced Quality: With a focus on doing things right the first time, the quality of the output improves, reducing the need for rework.
- Improved Team Morale: Lean encourages team involvement in process improvement, which can lead to higher engagement and satisfaction.
- Better Customer Satisfaction: Delivering what the customer values with efficiency leads to higher customer satisfaction.
- Cost Reduction: Less waste means less cost, both in terms of time and money.
Challenges in Implementing Lean
Implementing lean methodologies in project management can be akin to trying to conduct an orchestra where some musicians are still learning their instruments. Lean principles aim to maximize value by minimizing waste, but this simplification often meets resistance. There’s the challenge of over-process optimization – teams might focus too much on reducing waste to the point where they inadvertently start cutting into necessary processes, leading to quality drops or missed deadlines. Value identification can also be problematic; not everyone agrees on what ‘value’ means, leading to scope creep or misaligned priorities. Moreover, lean requires a high level of transparency and communication which, in many organizations, is easier said than done. Finally, lean thrives on empowerment and decision-making at the team level, which can be a significant culture shock for environments used to top-down management, potentially leading to resistance or misuse of newfound autonomy.
- Cultural Shift: Moving to a Lean mindset requires a cultural change, which can meet resistance. Teams used to traditional methods might find it hard to adapt.
- Training: Proper implementation requires training, which can be time-consuming and initially costly.
- Misinterpretation: Lean can sometimes be misinterpreted as merely cutting costs, which might lead to cutting corners, the very opposite of what Lean aims for.
Case Studies and Real-world Applications
Numerous organizations have seen significant improvements by applying Lean to project management:
- Software Development: Agile, which borrows heavily from Lean, has transformed how software is developed, focusing on delivering small, valuable increments quickly.
- Construction: Projects like the construction of the new airport in Denver used Lean to streamline operations, significantly reducing delays and costs.
- Healthcare: Hospitals have used Lean to reduce patient wait times and improve care delivery processes, focusing on patient value.
How Lean Doesn’t Apply to Project Management
Although it’s a good exercise to apply lean principles to project management, its roots in the manufacturing sector are such that you must understand its weaknesses in applying the method in a way it was not designed. Lean’s relentless focus on cutting out tiny inefficiencies one at a time (muda) in a production process sometimes doesn’t provide value to projects where the effort spent rooting out minute process inefficiencies don’t provide value when there are no corresponding economies of scale.
Conclusion
Lean methodology isn’t just a set of tools; it’s a mindset shift towards continuous improvement and customer-centricity. For project managers and teams willing to embrace this change, the rewards are substantial – not only in terms of project outcomes but also in fostering a culture of efficiency and innovation. The journey to becoming Lean might be challenging, requiring patience, training, and a willingness to experiment and adapt. However, in today’s fast-paced, resource-constrained world, Lean offers a compelling path to not just manage projects but to excel in them.
Leave a Reply