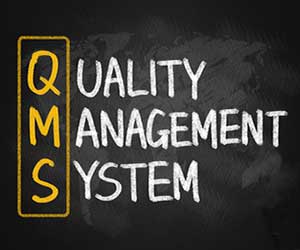
Are you unsure how you will obtain the quality of your project deliverables? Or what standards you need to measure against? Quality is one of the most important aspects of project management, and the production of a Quality Management Plan could be the answer you need.
According to the Project Management Body of Knowledge (PMBOK) a Quality Management Plan is a subset of the overall Project Management Plan. It can be a separate document or simply a section of the project management plan.
Its purpose is to ensure the quality of the project’s deliverables meet the acceptables standards as well as stakeholder’s expectations. It does this by specifying the quality standards the deliverables must meet and the actions that will be taken to get there. This ensures the maximum quality of the deliverables and the minimum cost of poor quality.
The quality management plan should contain the following three things. These items can be the individual headings within the document or they can be used as a guide:
- Quality Standards
- Quality Measurement
- Inspection
Quality Standards
In this section the standards by which the quality of the deliverables will be measured is specified. There are many places to obtain quality standards, and they can generally be categorized as follows:
- Internal company standards. There is a always a minimum standard of quality that is expected, even if it is simply the level of quality that clients, customers, and other stakeholders are used to receiving. This is worth writing down like any other quality standard so that the project team can strive to meet it.
- Regulatory requirements. Many projects require certain deliverables and a quality level that ensures passage through regulatory hurdles. If there is a question of whether or not it will pass regulatory scrutiny, this is something that should be communicated very well with stakeholders.
- Industry Standard Specifications. Almost every industry has standard of-the-shelf specifications which can used to measure quality.
- The American Society for Testing and Materials (ASTM) for construction.
- Institute of Electrical and Electronics Engineers (IEEE) for electrical work.
- Society of Automotive Engineers (SAE) for the automotive industry.
- Country-Specific Specification Bodies. In almost every country in the world a specification body publishes quality specifications for a wide variety of items:
- United States: American National Standards Association (ANSI).
- India: Bureau of Indian Standards (BIS).
- China: Standardization Administration of China (SAC).
- Quality Methodologies, like Six Sigma, Total Quality Management, Kaizen, Lean Manufacturing, and the like. Implementing a quality methodology rigorously can result in spectacular productivity gains with high quality products.
- Legal standard of care to the public (or simply, public expectations). Legal standard of care refers to the liability that a person incurs to the general public without having a contract with any one person. For example, an engineer has a legal standard of care to build bridges that do not fail, and can be held liable for damages to the person who is injured because of his/her actions. However, if the bridge does not actually fail but is perceived to be failing (cracking, loss of concrete, etc.), this clearly would render the project a failure due to public expectations. Both of these problems should be addressed in the Quality Management Plan to make sure they do not happen.
- External standards. Often the project sponsor or “owner” organization has standards that apply to all of their projects, such as safety standards for an oil company, or tolerance limits for a manufacturing company.
- Other stakeholder standards, like utilities, adjacent landowners, and other affected organizations.
Let me put this another way. All projects have quality standards or else they would not become projects. Somebody is expecting the deliverables and is therefore by definition expecting a certain quality level. As a minimum, this level of quality should be written down as a specification to the project team in the form of a Quality Standards section of the Quality Management Plan.
Quality Measurement
The selection of the quality standards for the project is performed during the project planning phase. During project execution then, the quality of the deliverables is measured against those standards.
This falls into two categories:
- Quality Assurance (QA) is the measurement of the quality systems and processes to ensure the quality standards are met.
- Quality Control (QC) is the direct measurement of the quality level of the project deliverables.
The distinction is often confusing, so allow me to elaborate. QA measures the process, while QC measures the deliverables. Quality Assurance is the measurement of the effectiveness of the systems which produce the products, while Quality Control is the measurement of the actual quality of the products coming out of the back end of that process.
For example, when paving a highway, QC would involve taking core samples at specified intervals to ensure the pavement on that stretch of highway meets the specifications. QA on the other hand, might involve measuring the number of defects or type of defects, or something that tells you how well the paving machine, or the process in general, is working.
The methods by which the quality of the deliverables will be measured should be specified in the Quality Management Plan and rigorously implemented during project execution. It should be as quantitative as possible, for example, a scale of 1-10, A to E, for every project deliverable. This allows the project manager at any time to communicate the current level of quality for the project.
Inspection
In order to ensure quality assurance (QA) or quality control (QC), there is almost always some form of inspection required. The Quality Management Plan should identify the following three things:
- Type of Inspection: The item that will be inspected and the inspection equipment that will be used. Also, the degree or level of inspection.
- Frequency: The time between inspections and spacing relative to unique events (such as replacement of machine supplies, etc.)?
- Criteria: The pass/fail criteria, or sliding scale (1-10) which will be reported.
Ideally an inspection form is developed or taken from a relevant source. It is important to be comprehensive and include all items necessary for a complete inspection, or else you could find yourself without the data you really want.
I would love to see an example of a real Quality Management Plan for a project.