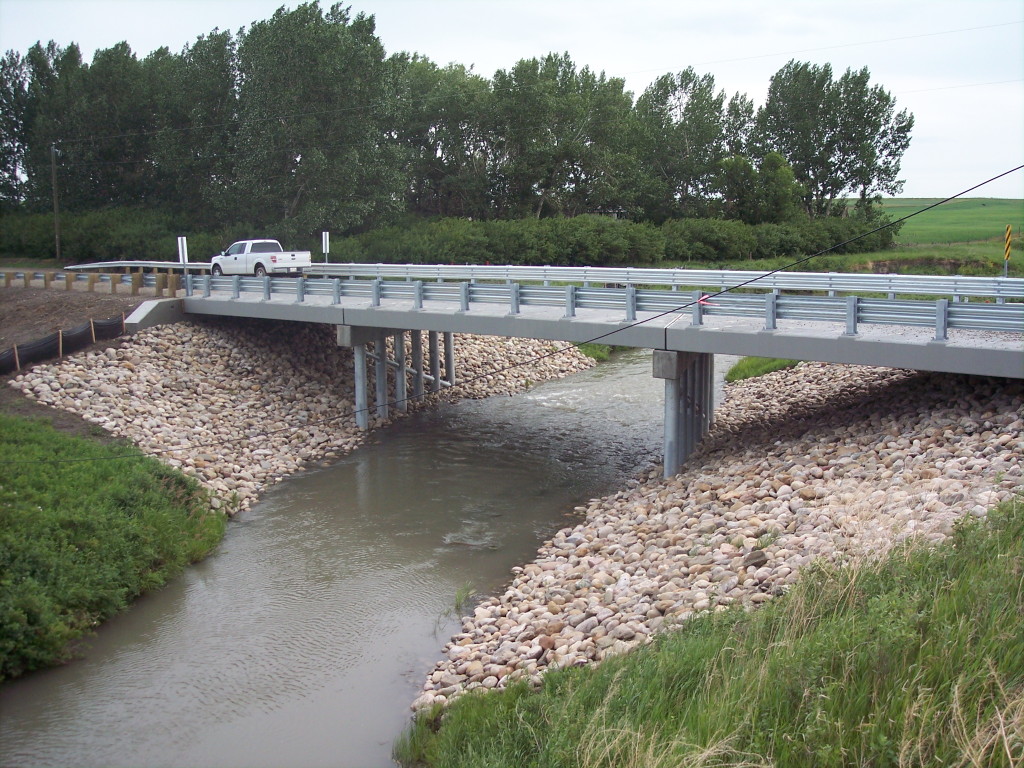
For us engineers, quality is a big deal. Industry standard quality control dictates that most documents and designs require a “second stamp” i.e. a reviewer who takes as much responsibility as the designer.
But what does a true project quality management plan look like? In this article, I will talk about project quality from the perspective of the project management industry. The following three step breakdown comes from the Project Management Body of Knowledge (PMBOK) by the Project Management Institute (PMI).
- Plan Quality
- Perform Quality Assurance
- Perform Quality Control
Plan Quality
At the outset of a project, an established set of standards should be defined against which the project’s deliverables should be judged. A proper quality plan should document what those standards are and the rating criteria to determine pass/fail, good/bad/ugly or something similarly well defined.
At Roseke Engineering, we have a standard project management plan which includes a quality management plan. Once a deliverable is complete, we provide a quality ranking by the project manager. Unfortunately with most engineering deliverables this is a difficult thing to do (how do you rate a preliminary engineering report that itemizes options for a bridge replacement?) but at least it forces the project manager to verify that the deliverable is of high quality. If the client asks questions that imply a low quality report, the project manager is at least held accountable to the project management plan, and thus the management of the company.
Quality planning should be performed in parallel with other processes. For example, meeting quality standards might dictate changes in the schedule, cost, or risk analysis for the project.
A quality plan can include the following items:
- Quality Metrics: A metric related to the quality objective could be that 0.1% of the widgets fail under a certain type of load. For many engineers, you don’t have the luxury of mass production. You could specify that 20% of engineers would find the design of a certain element excessive, which although not measurable, could give your engineers some direction.
- Quality Checklists: Many organizations have standardized checklists to ensure consistency in frequently performed tasks. Engineering reports and design drawings are rarely so different from previous projects that they don’t have some overlap. The quality plan can consult previous projects to itemize the project steps to ensure nothing is missed.
- Process Improvement Plan: A subsidiary of the project management plan, the process improvement plan details the steps for analyzing processes to identify activities which enhance their value.
- Project Documents: A great place to keep stakeholder registers, drawings, tenders, and so forth. Also, it is desirable to keep a register of document updates.
Perform Quality Assurance
Quality Assurance is defined as the process of auditing the quality requirements and the results from quality control measurements to ensure appropriate quality standards and operational definitions are used.
At specified points within the project, quality assurance audits should be conducted, which could mean simply that the project manager reviews the project quality requirements. This is an important step before the submission of major deliverables. For example, I’ve seen the client’s review personnel change during the course of completing a deliverable. If the new guy is picky about different things, maybe this is worth a “quality audit” before submission of the deliverable.
Perform Quality Control
Unlike quality assurance, quality control involves monitoring and recording the results against the established benchmark. It is more or less limited to the measurement of quality being produced by the project. It also includes tasks like attribute sampling, prevention, and tolerances, as well as inspection if necessary. The project management team should have a working knowledge of statistical quality control, particularly sampling and probability.
The project management plan should include some sort of quality measurement form/score against an established standard. Documenting the quality of work produced is essential to understanding how to improve the processes of your organization.
Leave a Reply