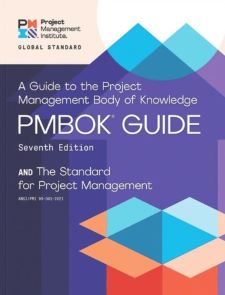
In the world of project management, the Project Management Body of Knowledge (PMBOK) highlights quality as a critical pillar of the Delivery Performance Domain.
Most projects focus the lion’s share of their efforts on time and cost. Project managers regularly land in the lion’s den when they overlook the third vital component of the project triangle: quality. A project’s success hinges on delivering a product or service that meets defined performance standards. Neglect quality, and even the most punctual, budget-friendly project can fall short.
Simply put, projects need to produce the final product or service at a certain quality level, or else the project is not a success.
Quality in the PMBOK
Quality is a subset of the Delivery Performance Domain within the Project Management Body of Knowledge (PMBOK). It focuses on the performance levels that are required to be met.
The PMBOK Guide specifies quality within the Delivery Performance Domain. There are three parts to effective quality management:
- Quality planning
- Quality control
- Quality assurance
Quality Planning
The first step is to decide what the quality standards are for the project. Generally, quality seems simple on the surface but many complexities lurk underneath. A project stakeholder wants or needs a certain quality level, and if that level is reached the stakeholder is satisfied. Sounds easy. But there is an associated cost, and often the stakeholder’s quality expectations are difficult to define. Also, in practice there are many ways to measure quality and plenty of ways to deal with quality issues.
Essentially, quality comes at a cost. There is a minimum quality level demanded by customers. Above that quality level, the project manager has the ability to invest money to increase quality, which must be balanced against the ability to increase the price of the product or produce savings (such as reduced scrap). But the lion’s share of a project manager’s time is usually spent on meeting the minimum customer expectations, a much more elusive goal than you’d think.
The PMBOK focuses on a concept called the Cost of Quality, which has four components:
- Prevention
Making an investment to prevent out-of-specification products from being produced results in savings to the project. This is generally called Quality Assurance. - Appraisal
Making an investment to determine how many products or services are out of specification so that their numbers can be reduced results in savings to the project. - Internal Failure
Finding defective products before they reach the customer. - External Failure
Finding defective products after they reach the customer.
There are many standards organizations whose sole purpose is to define quality standards, that cover the breadth of every industry. The American Society for Testing and Materials (ASTM) for construction, Institute of Electrical and Electronics Engineers (IEEE) for technology, and the International Standards Organization (ISO), just to name a few. Most projects aren’t doing anything highly unique or far removed from anything anyone has done before, and even if you are, these standards can be used as a guide to develop project-specific ones.
Quality planning should always result in quantitative, rather than qualitative, standards. That is, something should be measured. Although measurements at first seem pretty black and white, they can be the most elusive part of the process. Many project managers think they have quality planning covered until a few quality control measurements are taken, which brings up alot of questions about what constitutes acceptable, how it was measured, and what the results mean.
Quality Control
Once the standards have been defined, the quality control metrics are put in place. Quality control is an integral part of manufacturing and service industries, ensuring products meet specific standards before they reach the customer. It involves systematic processes like inspection, testing, and corrective actions to maintain consistency and reliability. Effective quality control reduces defects, minimizes waste, and enhances customer satisfaction. Techniques vary from statistical process control, where data is analyzed to detect production anomalies, to Six Sigma, which aims for near perfection in process outputs.
This step tends to seem basic on the surface, but again, the devil is in the details. How will quality be measured? How often? What is the acceptable range? What instruments will be used, and what range of error do they have? What happens when there is a non-compliance, that is, will the product be refurbished or scrapped, or will changes be made to the process?
Corrective actions are implemented as a result of quality control testing to increase the quality of the product or the success/failure rate.
Quality Assurance
Quality Control is often confused with Quality Assurance, but they serve a different purpose. While quality control directly measures the defect levels, quality assurance seeks to prevent the production of defects. It focuses on process improvement first.
Here are a few examples of tasks that represent quality assurance:
- Process Documentation: Establishing clear, detailed procedures for every aspect of production or service delivery.
- Training: Ensuring all team members are adequately trained and understand the importance of quality in their roles.
- Continuous Improvement: Adopting philosophies like Kaizen or Six Sigma for ongoing process enhancement.
- Audits and Reviews: Regular internal and external audits to ensure compliance with quality standards and to identify areas for improvement.
- Feedback Loops: Integrating customer and employee feedback into the QA process to evolve with market needs.
- Quality Metrics: Using data-driven metrics to measure quality performance and guide decision-making.
Implementing robust quality assurance systems not only safeguards brand reputation but also leads to cost savings over time by preventing errors at the production stage.
Project Quality Management is the 5th knowledge area within the Project Management Body of Knowledge (PMBOK). It contains the knowledge and processes required to ensure the highest quality products and deliverables are produced by the project. Although the highest quality should always be a goal, the highest grade is not necessarily so.
- Quality: The degree to which a set of inherent characteristics fulfill requirements.
- Grade: The performance specification to which a product is produced.
For example, a particular child’s toy might be high grade (many features, etc.), but if the parts break easily the quality could be unacceptable.
There are three processes within this knowledge area:
- Plan Quality Management. The selection of the quality standards and production of the Quality Management Plan.
- Manage Quality Auditing the processes being used to achieve the quality standards.
- Control Quality. Measuring the quality of the deliverables.
Plan Quality Management
This process involves the determination of the quality standards that govern the project deliverables and/or product and how the project will achieve compliance to those standards. Many projects have standards that are given to them directly, such as design standards for buildings. However, many other standards often exist which are not explicitly stated but expected to be complied with. The project manager could purchase the applicable standards from organizations such as ASTM, IEEE, or ANSI to ensure a complete set.
The main output of this process is a quality management plan which dictates the quality standards and outlines how those standards will be met as well as the quality assurance and quality control activities.
PMBOK, 6th Edition, Section 8.1.3.1, “Quality Management Plan”
The quality management plan is a component of the project management plan that describes how the applicable policies, procedures, and guidelines will be implemented to achieve the quality objectives. It describes the activities and resources necessary for the project management team to achieve the quality objectives set for the project.
The quality management plan may be formal or informal, detailed, or broadly framed. The style and detail of the quality management plan are determined by the requirements of the project.
Inputs
- Project Charter
- Project management plan
- Requirements Management Plan
- Risk Management Plan
- Stakeholder Engagement Plan
- Scope baseline
- Project Documents
- Assumption log
- Requirements documentation
- Requirements traceability matrix
- Risk register
- Stakeholder register
- Enterprise environmental factors
- Organizational process assets
Tools & Techniques
- Expert judgment
- Data gathering
- Benchmarking
- Brainstorming
- Interviews
- Data analysis
- Cost-benefit analysis
- Cost of quality
- Decision making
- Multicriteria decision analysis
- Data representation
- Flowcharts
- Logical data model
- Matrix diagrams
- Mind mapping
- Test and inspection planning
- Meetings
Outputs
- Quality management plan
- Quality metrics
- Project management plan updates
- Risk management plan
- scope baseline
- Project documents updates
- Lessons learned register
- Requirements traceability matrix
- Risk register
- Stakeholder register
Manage Quality
Manage Quality is the process of auditing the quality requirements and the results from quality control measurements to ensure that appropriate quality standards and operational definitions are used. The quality audits test and/or confirm that the system is functioning correctly. Quality assurance should always be based on a foundation of continuous improvement.
Inputs
- Project management plan
- Quality management plan
- Project documents
- Lessons learned register
- Quality control measurements
- Quality metrics
- Risk report
- Organizational process assets
Tools & Techniques
- Data gathering
- Checklists
- Data analysis
- Alternatives analysis
- Document analysis
- Process analysis
- Root cause analysis
- Decision making
- Multicriteria decision analysis
- Data representation
- Affinity diagrams
- Cause-and-effect diagrams
- Flowcharts
- Histograms
- Matrix diagrams
- Scatter diagrams
- Audits
- Design for X
- Problem solving
- Quality improvement methods
Outputs
- Quality reports
- Test and evaluation documents
- Change requests
- Project management plan updates
- Quality management plan
- Scope baseline
- Schedule baseline
- Cost baseline
- Project documents updates
- Issue log
- Lessons learned register
- Risk register
Control Quality
Quality Control is the process of monitoring and recording results of executing the quality activities to assess performance and recommend necessary changes. In short, it is the measurement of defects.
Inputs
- Project management plan
- Quality management plan
- Project documents
- Lesson learned register
- Quality metrics
- Test and evaluation documents
- Approved change requests
- Deliverables
- Work performance data
- Enterprise environmental factors
- Organizational process assets
Tools & Techniques
- Data gathering
- Checklists
- Check sheets
- Statistical sampling
- Questionnaires and surveys
- Data analysis
- Performance reviews
- Root cause analysis
- Inspection
- Testing/product evaluations
- Data representation
- Cause-and-effect diagrams
- Control charts
- Histogram
- Scatter diagrams
- Meetings
Outputs
- Quality control measurements
- Verified deliverables
- Work performance information
- Change requests
- Project management plan updates
- Quality management plan
- Project documents updates
- Issue log
- Lessons learned register
- Risk register
- Test and evaluation documents
Leave a Reply