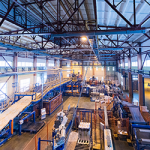
The japanese language contains a word that is so powerful and expressive that it has gained widespread acceptance in the manufacturing industry: muda. Muda means waste, but it's more than that. It embodies the full essence of inefficiency, uselessness, and squandered potential. The word muda has become a cornerstone of lean manufacturing, which originated in Japan … [Read more...]