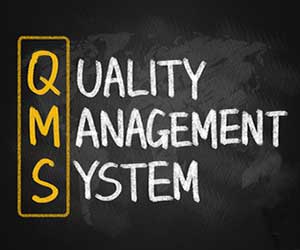
Quality isn’t free. The American Society for Quality (ASQ) suggests that the Cost of Quality is usually around 15 – 20% of sales, often as high as 40% in some organizations.
From the resources spent preventing mistakes to the fallout of fixing them, the cost of quality shapes how businesses operate and compete. Far from being just a buzzword, quality is a real, tangible cost embedded within a process, a financial lever that can drive success or drag a company down.
Clearly, it is imperative that all project managers and business leaders know what their cost of quality is, and how to prevent errors and omissions from hurting your business.
What is the Cost of Quality?
Cost of Quality (COQ) is a measure of the cost an organization faces due to the production of substandard products and services.
What are the 4 Parts of the Cost of Quality?
It has 4 components:
- Prevention
- Appraisal
- Internal Failure
- External Failure
The first two are proactive, that is, they prevent the production of defective products in the first place. The latter two are reactive and involve managing the defective products once they have been produced.
It can be expressed in numerical form as a percentage of sales, and can be mathematically calculated using the above four factors:
COQ = Prevention + Appraisal + Internal Failure + External Failure
Prevention
The best way to lower the cost of quality is to prevent poor quality products or services from being produced in the first place. For example,
- A vehicle manufacturing company launches a program to inspect all of the robotic arms for wear and tear to reduce the instances of assembly line downtime.
- An engineering firm develops a manual which governs the production of a specific type of report.
- A shipping company develops an I.T. product which reduces delayed shipments.
This is where the biggest gains are possible. It is often the most underrated yet productive part of the COQ equation. Investment in prevention results in higher customer satisfaction and project success, which is often difficult to measure but at the same time the most important factor to corporate success.
Naturally, there is a trade-off when investment is made in prevention (at the front end) which reduces the number of defective products coming out of the back end. So an investment in prevention is not purely a cost proposition. After increasing product quality, support and technical assistance staff can be reduced once the results are achieved.
Here are a few ideas to include in an effective prevention program:
- Training
- Evaluation of Suppliers
- Quality Assurance audits
- Quality planning
- Product reviews
- Lessons learned analyses
- Quality-related information systems
Prevention and quality assurance are joined at the hip. Quality assurance audits should be done randomly or systematically on any existing process, with the goal of improving the quality of the product being produced. Most prevention programs fall into this same definition.
Appraisal
This part of the equation represents the cost of measuring quality throughout the production process. For example,
- A construction contractor inspects the building materials that arrive on the job site.
- A watch manufacturer tests one out of every 100 watches over 7 days to ensure the time is correct.
- A bakery inspects one out of 10 loaves for conformance to the specifications.
Appraisal also has a twin, quality control. Quality control measures the results coming out of a production process to determine what is going wrong and how badly. Appraisal often falls within this definition as well. Thus, a strong background in quality assurance (QA) and quality control (QC) is the first step to establishing the cost of quality.
Together, prevention and appraisal represent the internal cost of ensuring that quality products are produced. They are proactive. They have been called the cost of good quality and should be an integral part of any production process. If you are in charge of a production process that does not have a formal prevention and appraisal process, you should start one immediately.
On the flip side, the cost of poor quality, sometimes called COPQ, is the result of correcting failure, that is, products that do not meet the specifications. It is reactive and indicates a poor prevention and appraisal system.
Internal Failure
This element refers to the cost of defective products that do not reach the customer. For example,
- A steel mill rejects products that do not have the chemical composition specified by the customer.
- A senior accountant reviews the data and discovers mistakes which must be corrected.
- A plastics manufacturing plant rejects 1.7% of its production.
These defective products are caught by the organization’s quality control activities and are either rejected or repaired. The quality control itself falls under Appraisal (above) but the cost of the repair, or the value of the rejected product, is classified as internal failure costs.
External Failure
This factor in the equation represents external issues after the product has left the organization, such as:
- An electronics manufacturing facility receives a higher number of warranty returns
- A railway must delay shipments due to new track that was poorly laid and didn’t pass ultrasound testing.
- The opening of a new highway is delayed because of poor planning and scheduling.
The direct costs of failure are usually just a small part of the the total cost to an organization, even if it’s the main focus of the project team. Loss of future business and reputation can be extremely costly but difficult to define. Lawsuits and malpractice claims due to defective products or services can be a major one-time cost down the line.
“Due diligence” is often a major consideration in the award of damages, and a poor reputation for quality usually makes a case difficult to win. Negotiations with suppliers and clients also take a turn for the worse, with future cost implications.
Typical Values
According to the Quality Digest, some typical values for Cost of Quality in the manufacturing industry are as follows:
Industry | COQ as a Percentage of Sales |
---|---|
Aircraft engines / engine parts | 5.4 – 6.3 |
Aircraft parts | 4.5 – 8.6 |
Aluminum die castings | 5.3 – 7.1 |
Aluminum extruded products | 4.4 – 7.0 |
Automotive stampings | 5.3 – 7.0 |
Engine parts | 5.0 – 7.1 |
Fasteners | 6.2 – 7.1 |
Forgings – non-ferrous | 5.9 – 6.9 |
Mobile homes | 4.8 – 5.3 |
Motor home / automotive bodies | 4.3 – 5.4 |
Motor homes | 4.8 – 5.3 |
Automotive parts / accessories | 6.1 – 8.0 |
Motorcycles, bicycles / parts | 6.1 – 6.8 |
Motors / generators | 5.2 – 6.1 |
Storage batteries | 5.1 – 5.4 |
Tubes / tires | 6.9 – 8.0 |
Travel trailers / campers | 4.9 – 5.9 |
Truck / bus bodies | 4.3 – 5.4 |
The ideal place is on the low end of the industry average values reported here. A COQ of zero is not the goal, because you need to spend some money on prevention and appraisal (quality assurance and control). If you are on the high end of the range, you are not as efficient as your competitors. If you are below the range, you can probably increase spending on customer satisfaction and still being cheaper than your competitors.
Example
Let’s say you are a furniture manufacturer with $1 million in sales. How do you calculate your cost of quality? Each of the four items should be itemized and listed. Man-hours and equipment can be calculated for each item.
- Prevention: Sending workers to training and improving processes to reduce defects.
- Appraisal: The hours spent on quality control processes, such as inspection before shipment, inspection of paint, and wood working equipment.
- Internal Failure: The cost of raw materials, labor and production for rejected items, or the cost of fixing them.
- External Failure: Cost of warranty replacements, including the office work required to maintain the warranty program.
Category | Description | Cost | COQ ($1 million in sales) |
---|---|---|---|
Prevention | Send workers to yearly workshop | 10 employees @ $2,500 = $25,000 | 2.5% |
Appraisal | Inspect equipment every friday evening | 1 hour @ $45/hr x 52 weeks = $2,340 | 0.23% |
Internal Failure | Cost of fixing rejected items | 4 hours/week $ 45/hr x 52 weeks = $9,360 | 0.94% |
Failure | Warranty returns | 15 warranty returns per year @ $5,500 = $82,500 | 8.25% |
COST OF QUALITY | $119,200 | 11.92% |
According to the table above, you are spending significantly more on quality than your competitors.
Let me know in the comments what your cost of quality is, and how it affects your business.
That’s good to know that appraisal and quality control helps to make sure that you have a good quality product. I could see having both of those could also affect the quality of the equipment that you own already. If you have your equipment appraised then you can know what is wrong with it and the quality control would be repairing it.
I found it interesting that you state that prevention and appraisal represent the internal cost of ensuring a quality product. My brother has been looking for ways to increase the quality of his part production. I will send him this information so he can make sure to find an industrial equipment appraisal service to help him.